Die Casting Machining: Unlocking Precision and Efficiency in Metal Fabrication
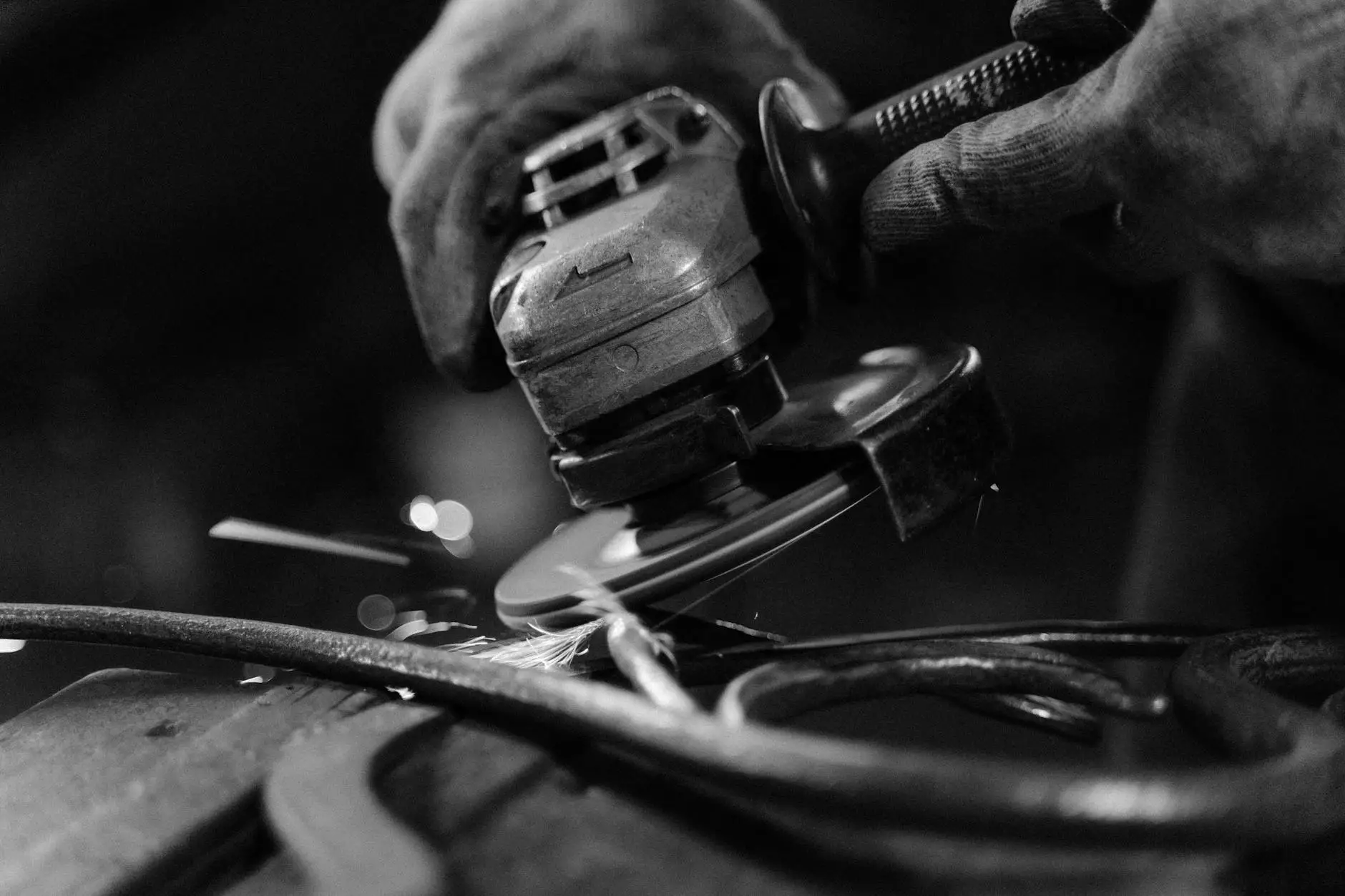
In the world of metal fabrication, few processes offer the same level of precision and efficiency as die casting machining. This manufacturing technique is a game-changer for numerous industries, providing the ability to create intricate shapes and designs with minimal waste and unrivaled accuracy. In this article, we will dive deep into the world of die casting machining, exploring its processes, advantages, applications, and future trends that promise to elevate the manufacturing landscape.
What is Die Casting Machining?
Die casting machining is a metal casting process that involves forcing molten metal under high pressure into a mold cavity. This method is ideal for producing high volumes of parts with excellent surface finish and dimensional accuracy. The process is primarily used for metals such as aluminum, zinc, copper, and magnesium.
The Die Casting Process
- Mold Preparation: The die or mold is created, typically from steel, and is designed to withstand high temperatures and pressures.
- Melting Metal: The chosen metal is heated until it becomes molten, reaching specific temperatures that vary depending on the type of metal.
- Injection: The molten metal is injected into the mold cavity at high pressure, filling the space rapidly to ensure that the mold outlines are filled.
- Cooling: Once the metal has filled the mold, it is allowed to cool and solidify, taking the shape of the mold.
- Ejection: After cooling, the solidified part is ejected from the die, usually with the help of ejector pins.
- Trimming and Finishing: Any excess material, such as flash, is trimmed away, and finishing operations may be performed to enhance the surface quality.
Advantages of Die Casting Machining
The benefits of utilizing die casting machining in your production processes are numerous:
- High Precision: Die casting creates parts that are dimensionally precise, making them suitable for tight tolerance applications.
- Superior Surface Finish: The process yields parts that require minimal finishing, reducing time and costs associated with secondary operations.
- Material Efficiency: Die casting minimizes waste, as the method produces near-net shape parts that reduce excess material removal.
- Durability: Die-cast items possess a strong, dense structure, contributing to their overall durability, making them suitable for various applications.
- Rapid Production: The process is conducive to mass production, allowing manufacturers to produce large quantities of parts in a short timeframe.
- Engineering Flexibility: Complex geometries and intricate designs can be achieved, offering engineers and designers a wide range of creative possibilities.
Common Applications of Die Casting Machining
Die casting machining is employed across various industries, demonstrating its versatility:
- Automotive Industry: Components such as engine blocks, transmission cases, and other critical parts are manufactured using this process.
- Consumer Electronics: Housings for devices such as smartphones, laptops, and game consoles are often produced via die casting.
- Aerospace: Components that require strict tolerances and reliability are created using die casting techniques.
- Industrial Machinery: Various parts and components are produced for machinery and equipment used across multiple sectors.
- Medical Devices: Precision components for medical equipment benefit from the accuracy of die casting machining.
Challenges in Die Casting Machining
While the advantages of die casting are substantial, there are challenges that manufacturers must navigate:
- High Initial Costs: The creation of dies can be expensive, which may deter smaller manufacturers.
- Metal Limitations: Not all metals are suitable for die casting, which limits material choices.
- Complex Designs: While die casting allows for intricate shapes, overly complicated designs may pose manufacturing difficulties.
The Future of Die Casting Machining
As technology evolves, so too does the field of die casting machining. Some emerging trends include:
- Automation and Robotics: Increased automation in die casting processes enhances efficiency and reduces labor costs.
- 3D Printing: The integration of additive manufacturing techniques in creating die designs offers more flexibility and customization options.
- Sustainability Practices: Advances in recycling and material efficiency are making die casting processes more environmentally friendly.
- Smart Manufacturing: The incorporation of IoT technology enables real-time monitoring and optimization of the die casting processes.
Conclusion
In conclusion, die casting machining represents a critical component of the modern metal fabrication industry. Its ability to produce high-quality, precision parts quickly and efficiently has made it a preferred choice for manufacturers across diverse sectors. As the industry continues to evolve, the ongoing advancements in technology, material science, and sustainability practices will ensure that die casting remains at the forefront of innovative manufacturing solutions.
For businesses looking to leverage the benefits of die casting, partnering with reputable metal fabricators such as DeepMould can provide significant advantages in terms of expertise, advanced machinery, and a commitment to quality standards. Embracing die casting machining not only enhances production capabilities but also positions businesses to meet the demands of an ever-evolving marketplace.